Going green has the potential to be a wise business decision for the manufacturing industry. In fact, it seems many manufacturers are making the jump to more sustainable processes and business operations.
Traditional manufacturing processes are based on a linear model of consumption—that is, finite energy resources are consumed during the production process and many products are often discarded.
But as concern grows regarding these finite resources and as costs go up, pivoting to green manufacturing is one way businesses can preserve these resources and keep costs down.
Resources aside, we’ve also seen a rise in consumer boycotts regarding unsustainable manufacturing. Plus, given unpredictable weather and geopolitical events, a green pivot also allows for a degree of decoupling from inconsistent supply and production chains, giving you more independence and control. This guide aims to provide a comprehensive overview of green policies and workflows in modern manufacturing.
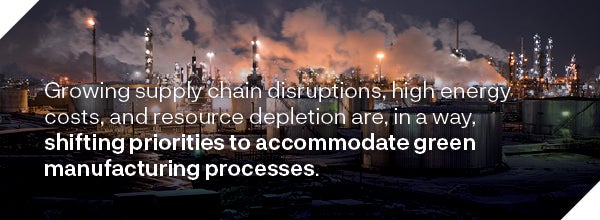
Understanding Current Manufacturing Process Shortcomings
The traditional structure of manufacturing tailors operations toward profitability and puts production efficiency above all else. However, growing supply chain disruptions, high energy costs, and resource depletion are, in a way, shifting priorities to accommodate green manufacturing processes.
To understand exactly why traditional manufacturing is no longer viable, you may want to examine two key tenets of production: energy consumption and pollution.
First, the high energy consumption required to operate factories, warehouses, and supply chains may be necessary for modern society. But the reality is that current modes of energy production are finite.
Second, under traditional manufacturing structures, pollution wasn’t a major public concern. However, the public is now shedding light on the pollution concerns of traditional manufacturing. While green manufacturing has become a buzzword, the meaning remains prescient, sustainable practices should be considered to secure a brighter future for the industry.
With this in mind, the question becomes how to maintain modern modes of living without traditional manufacturing.
Green manufacturing presents one of the most compelling answers to this quandary. It eliminates the toxic pollution and unsustainable energy consumption that may be plaguing the manufacturing industry. Yet it also enables the production of both essential and luxury goods to carry on. In this way, the industry can create stable operations that may have a viable long-term outlook.
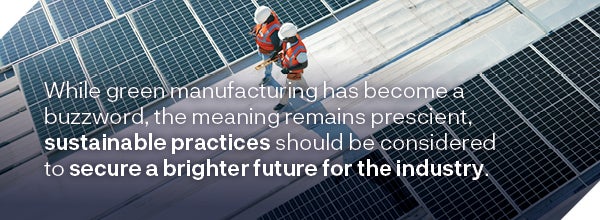
Assessing Your Current Workflow
While the need to adopt green manufacturing processes may be clear, the best way to go about the operational transition can be more nebulous.
Your manufacturing process has likely developed unique components and processes that cater to specific markets or locations. Uncritically overhauling the balanced workflows you already have in place could result in disaster for the company. So, the implementation of green practices may need to be more strategic.
If you’re interested in developing green operational habits, you may want to begin with a sustainability assessment. This is a critical examination of your current workflows to identify and improve targeted areas. Specifically, you might want to consider looking at areas like energy consumption, raw material usage, waste management, and supply chain practices in isolation. This could help you pinpoint where more sustainable improvements could be made.
Say you identify that one step in your manufacturing process is particularly energy-intensive. You could improve it by switching the power source for this specific workflow to a renewable source. You might also:
- Implement a recycling program for key components to improve waste management
- Switch to local suppliers to minimize the carbon footprint of your supply chain
- Look for raw material alternatives to use in production
Of course, the depth of your plant’s sustainability assessment will depend on your green manufacturing transition timeline. So, you can quickly look into more nuanced processes like specific product life cycle assessments to further improve sustainability. This process looks at the entire life of a single product, from where its raw resources are sourced to where it ends up after consumption.
Such a granular but comprehensive analysis helps you identify the most environmentally detrimental points of the product’s life cycle so you can brainstorm potential solutions.
Meeting Your Sustainability Goals: Understanding Green Manufacturing
In its broadest sense, green production aims to eliminate the unsustainable, toxic, and wasteful elements of the manufacturing process. But in practice, this can manifest in a lot of different initiatives.
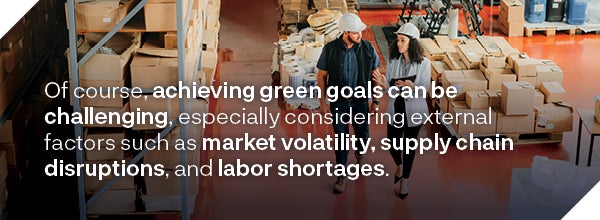
For instance, a factory that closes the loop on its water consumption system by treating and reusing its own wastewater is implementing a form of green manufacturing. The same can be said for a factory that switches a plastic component for a biodegradable material. Similarly, a company could improve efficiency on the factory floor and also cut back on energy consumption by incorporating Internet of Things (IoT) Industry 4.0 devices.
Of course, achieving green goals can be challenging, especially considering external factors such as market volatility, supply chain disruptions, and labor shortages. The effort required to move toward a green manufacturing model also needs to be in alignment with the goals of shareholders and stakeholders.
Luckily, sustainable manufacturing can generate many material and quantifiable benefits. For instance, you may qualify for potential governmental incentive programs and tax benefits if you meet set sustainability benchmarks.
At the same time, minimizing waste and reducing energy consumption can result in significant cost savings. Plus, this has the added benefit of helping companies reach and maintain compliance standards and avoid fees and penalties.
However, the public perception boost may be the most intangible but extremely beneficial perk of green manufacturing. Consumers—especially younger generations —are increasingly concerned about sustainable practices. And they want products and services that share these values.
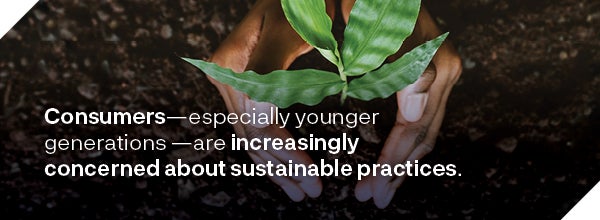
Green Manufacturing Strategies
Manufacturers already know how to adapt to innovative new technologies and production processes. After all, the industry has been under a near-constant state of evolution since Ford famously introduced the concept of an assembly line.
Production in any sector is highly contingent on market demands and entirely dependent on the strength of the supply chain.
But the concept of green manufacturing is still a sizeable shift in operations, workflows, and perhaps even priorities. So, even if you can adapt quickly, you may find aspects of the green manufacturing transformation difficult to contend with.
With this in mind, you might consider allocating additional energy and resources to the strategic planning phase of each sustainability project. This way, you’ll be able to communicate the process to employees and shareholders more clearly. You can also state the intended value that the effort generates for the plant in a more straightforward and compelling manner.
Needless to say, getting all interested parties on the same page at the outset can prevent headaches and confusion down the line. It may even smooth out the transition process.
The first step of planning is often learning the ins and outs of the initiatives you’ll be enacting. This way, you can more easily fit the theoretical framework to your specific plant’s unique needs. Plus, planning down to the most granular detail of each step toward a more sustainable production process may help you foresee and circumnavigate potential issues before they disrupt operations.
The following strategies may help ease the implementation of green manufacturing principles:
Sourcing Sustainable Materials
In its most basic sense, sourcing more sustainable materials means changing product components to use fewer environmentally harmful substances. There are several different ways you can do this.
For instance, you may swap the materials used in components of a product to less harmful iterations. You may also reduce the amount of raw materials you use in production or change the material technologies you use.
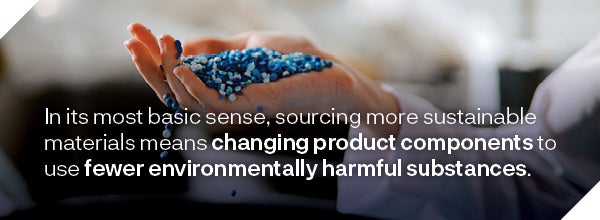
All these potential process alterations are excellent first steps toward green manufacturing. But they aren’t the end-all, be-all of green materials sourcing. In fact, environmental, social, and governance (ESG) goals are currently developing stricter guidelines regarding the transparency and ethics of raw materials’ origins.
A more comprehensive approach to strategic green materials sourcing may need to incorporate the idea of provenance or trace the origins of materials. This means that the origin point of the materials that go into your product would be fully traceable to consumers, down to the carbon footprint of their extraction and shipment.
Consumers are increasingly paying attention to these factors when they make purchasing decisions. So, companies with proven sustainable practices at each end of their supply chain may be the first choice of many buyers.
Redesigning Products
In some cases, switching materials to more sustainable sources or reducing the quantity of raw resources used in production will require you to re-engineer the product. This often means one of two things:
- Figuring out how to maintain the integrity of the product with different materials
- Finding ways to alter or extend the life cycle of the product
Some companies have found that renting or leasing their products results in a vastly extended life cycle as compared to selling items outright. Plus, this alternative business model allows you to potentially cut down production costs significantly by extracting greater value from each individual item.
Of course, some products aren’t conducive to this business model. So, if you can’t design the product’s life cycle, reimagining the component material configuration may be the most suitable option.
One common green manufacturing product redesign initiative is to make the most resource-intensive components of the product recyclable. For instance, manufacturers that work with lithium-ion batteries may often initiate recycling programs to close the loop on the most environmentally detrimental aspects of their production. This way, valuable resources like lithium don’t end up in a landfill but continue to fulfill the purpose of their extraction in the first place.
Achieving Energy Efficiency
Cutting down energy use is one of the most important initiatives for green manufacturing for a few reasons. Production is one of the most energy-intensive processes in the world. In addition, manufacturers benefit immediately from a reduction in costs. This makes it easy to bring the initiative to shareholders and stakeholders.
Advancements in manufacturing automation and machine learning can help grant you greater visibility into energy consumption during the production process. As a result, you may cut down consumption at the most wasteful points.
At the same time, improvements in how renewable energy resources are applied make switching to sustainable sources a more practical option. You can source your power from many renewable sources or develop your own solar farm on-site to augment your energy consumption.
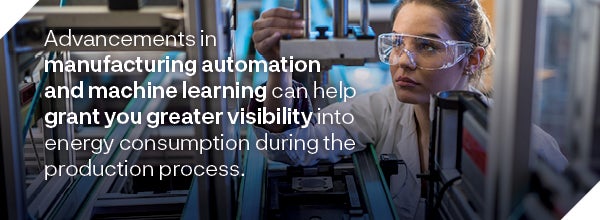
Power purchasing agreements (PPAs) allow manufacturers to fix the price of their renewable energy supply for anywhere between 15–20 years. So, while sustainable energy may be more costly at the moment, PPAs could be a wise investment for the future, considering the current pace of inflation.
Either way, technology is proving to make green manufacturing a much more obtainable objective, especially regarding energy consumption.
Reducing Waste
There are a wide variety of strategies you can implement to reduce waste in the production process. Basically, any form of output that degrades, clutters, or harms the environment can be considered a form of waste. However, there are as many potential ways to cut down waste as material outputs result from production.
For instance, you could reduce water waste in production by looking into new processes and workflows that eliminate its use. You may also explore closed-loop production cycles to reduce material waste or try a reshoring initiative to cut wasteful emissions in the shipping process.
The most impactful initiative to reduce waste in your factory will depend on which steps in the process are most harmful to the environment. So, if waste reduction is to be your green manufacturing strategy for the near future, you may want to consider conducting a critical examination of which parts of your production process yield the most waste.
This way, you can make sure that the results of your efforts have the biggest impact. Plus, this brings the added benefit of fostering well-earned appreciation when you share these initiatives with the public.
Integrating Green Manufacturing Into Your Workflow
Once you’ve determined which green manufacturing strategy or initiative to pursue, the next step is to create a detailed execution plan. There are likely many moving parts and people within your company that will be impacted by the change. A good starting point is often to communicate the process through employee engagement and training.
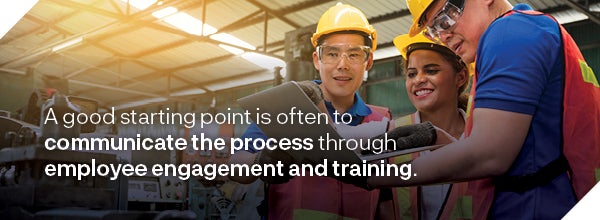
At first, the training can help focus on fostering a sense of a shared mission around the project. For instance, you might highlight how different roles in the change help achieve sustainability. The training process should also incorporate detailed communication regarding how employees will operate any new potential machinery or equipment.
It can also be helpful to provide extensive resources throughout the entire change and implementation process. This gives workers somewhere to turn if there are snags in the process or confusion around new workflows.
Finding the right technological solutions is also of paramount importance when it comes to sustainability in manufacturing. This may include energy-efficient machinery, waste reduction systems, and automation tools that help minimize environmental impact.
The exact type of equipment you need will depend entirely on your sustainability goals and the unique factors of your production. But regardless of what equipment you’re looking into, researching the investment ahead of time can help you ensure that the machinery will deliver on its promises.
Finally, there are a growing number of regulations surrounding green manufacturing around the globe. So, while you’re strategizing your green initiatives, it may be best to research the local rules and regulations you’re under. This can help you avoid heavy fines and penalties. At a base level, you can start by understanding the legal requirements related to waste management, emissions, and resource use.
Overcoming Challenges in Green Manufacturing
As with any organizational-level change, the transformation is likely to be complex and somewhat difficult to manage. However, by preparing for the most common challenges that crop up during green manufacturing projects, you may be able to prevent or mitigate some issues before they occur.
One of the most common challenges you may encounter immediately is resistance to change from employees and leadership. You can try to overcome this initial hesitation by crafting a compelling business case ahead of time.
Another key issue you may face surrounds developing ways to track the progress of your green initiatives. Technology such as IoT sensors and analytics software can help you accurately track performance against sustainability goals. This way, you have solid progress markers that you can share both internally and externally to foster excitement regarding the success of the project.
You may also face challenges integrating new and complex technologies with your existing workflows and digital systems. However, you can mitigate these issues by partnering with a technology provider that offers support and training to its clients. In addition, you might consider pilot-testing new technologies before implementing them at scale to ensure that they fit your vision and current infrastructure.
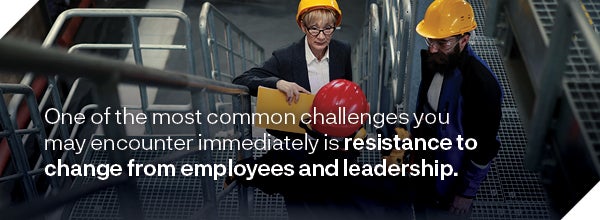
Perhaps most importantly, you may have to tackle the thorny problem of financing the whole effort to get the project off the ground. Green manufacturing often requires significant upfront investments in new technologies, equipment, and training.
Leaders can overcome the natural hesitation behind this investment by communicating the long-term return on investment (ROI) from the project’s energy efficiency and waste reduction. At the same time, you can look for grants and subsidies to reduce costs. You may also want to consider partnering with a banker to make the most of the initial investment.
Understanding the Financial Implications of Green Manufacturing
Green manufacturing is likely to be the future of production across sectors. By bringing processes closer to home and opting for sustainable resources, manufacturers can gain a competitive edge.
Factors like cost savings through energy-efficient technologies, enhanced brand reputation with eco-conscious consumers, and compliance with environmental regulations all make sustainability a more attractive and financially viable option. Plus, the shift toward greener technology may also open new markets, which could help you scale up.
However, there’s no getting around the fact that the transition to greener workflows often requires a significant upfront investment. That said, there are some potential avenues to reduce the initial costs and improve the returns of this investment.
Accessing these financial avenues takes customized advice from a knowledgeable business banker. A reliable bank partner like Premier Valley Bank, a division of HTLF Bank can provide crucial resources and guidance. Reach out and start a conversation today.
These links are being provided as a convenience and for informational purposes only; they do not constitute an endorsement or an approval by HTLF of any of the products, services, or opinions of the corporation or organization or individual. HTLF bears no responsibility for the accuracy, legality or content of the external site or for that of the subsequent links. Contact the external site with questions regarding its content and privacy policy.